So many times I got in a heated argument with the warehouse team over their requests. Was I always right? I doubt it. This article will try to find several ways you can resolve your dispute with the warehouse team.
Who wants what
Let us start with the goals of procurement and warehouse:
Subject | Procurement | Warehouse |
Stock levels | High, at least a month | Short, not more than for a week |
Order to delivery time | Long, so the vendor can find the cheapest transport option | Short, as there is not much stock available |
Variety of items | To cover 80% of all orders | To cover only the top 20% of items |
It is very difficult to determine “who is right” in such discussions. Both parties have very valid arguments for their recommendation. In both cases, there will be a financial impact on the company based on the final decision.
Here are a couple of solutions aiming to find objectively:
- The right level of stock
- When should we place the next order
- What would be the right quantity of the order
The ABC method
The ABC method draws its logic from the Pareto Principle. You can read more in detail on the link below. It is also known as the 80/20 rule, defining that 20% of the causes bring 80% of the results.
In Supply Chain we use the 80/20 rule defining that 80% of the throughput of the stores comes from 20% of the items.
Hence, we are separating our inventory into roughly three groups:
A category, the top 20%. We need to always have these items in stock. They are also known as fast-moving stock.
B category is the stock that has some movement, usually at least once a year. Those are items where we keep minimal or no stock. It is important to know them, so procurement can line up vendors stocking those items. The stock is ordered in minimal possible quantities only, unless it has a long lead time. In this case, some minimal stock is kept
C category is the non-moving stock. This stock had no movement in the last year. We will aim to utilize it wherever possible or sell it back to the vendor. If it takes significant space it may even be discarded. During these long holding times, the cost of storage may exceed the cost of the item itself.
This system is the easiest to implement, but it has a couple of negative sides. It reacts slowly to changes in requirements. Secondly, it does not take into account seasonal changes. Winter clothing may be considered slow-moving in August, but the situation will completely change in November. As a result, you will not have sufficient stock to cover the demand.
Minimum order quantity (MOQ) formula
If we have sufficient data, we can calculate our minimum and maximum stock levels, as well as the reorder level
Here is a simple example:
Reorder point / Reorder level | When to order |
EOQ | Size or quantity of order |
Reorder level formula: | (Lead time x average daily consumption) + safety stock |
|
|
Example: |
|
Lead time | 12 days |
Average daily consumption | 100 units |
Safety stock to be maintained at 7 days of consumption |
|
|
|
ROL= | (12 days * 100 units) + (7 days * 100 units) |
| 1900 |
EOQ – Economic order quantity can be calculated in 3 ways:
a) Based on the number of deliveries your company would like to receive in a month/year
Annual Consumption | 30000 |
We want to place only 2 orders in 1 month from one vendor |
|
Therefore, the total number of orders | 24 |
Order Quantity | 1250 |
b) Taking into consideration order and holding costs
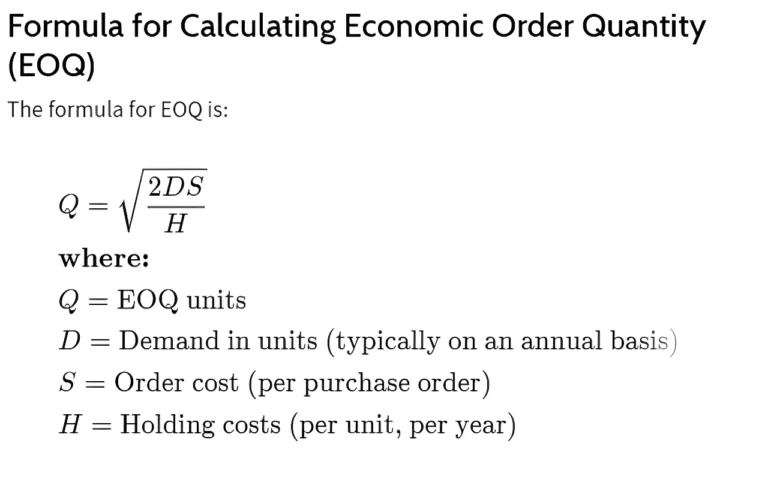
a) Based on the Minimum order quantity from the vendor
In some cases, the supplier will inform you about the Minimum Order Quantity (MOQ). This is the least quantity where they will accept the orders. Usually trying to reduce the MOQ will result in a significant cost increase. The supplier will state that he needs to push to you the costs of preparation of the machines.
If the calculated EOQ is below the MOQ given by the supplier, you will have to change your plan based on this limitation.
Based on orders from end user
This is the only way if you do not have sufficient data to use formulas to define your minimum stock and reorder levels. It also works very well if:
- There is a significant change in consumption patterns due to changes in the production, or expansion
- You have a brand new product or service, where you do not have any historical data
- Your output is project-based: construction, single-item manufacturing, events and similar services. Here you know most of the requirements in advance and the request never (or rarely) repeats exactly with the same specification.
You will request the end users to provide their plans or estimations. Working backwards, you will request the production to create their needs. And then you will make the time plan for deliveries. Take into consideration the lead time and agree with all stakeholders on the buffer levels. Using the Critical path method, described in this article you will determine the order times as well as the safety stock. If the sales team planned well this results in a quite smooth operation.
Advanced planning
Some manufacturing companies have set production plans for three months, or even longer. If this is the case, you are lucky. Procurement needs to fix the prices for a specified time frame. The warehouse will provide the schedules for the items. The warehouse serves as an unloading/quality control area. The only stock kept is a small quantity of safety stock in the case of delays in transport. Moving forward, this will become “just in time” delivery, once you have found the suitable suppliers and entered into partnership agreements with them.
So, here are some tools. Once you have found the one that suits your organization, stick to it. But do not set the rules in stone. The requirements change and there must be a revision of the data at least annually.
Secondly, there is no perfect system. IKEA plans 84 weeks in advance. They use advanced software systems and a whole army of scientists and analysts. Yet, from time to time, the item you are asking for is “out of stock due to high demand”. Don’t beat yourself up if you run out of stock. Fix it and increase the safety stock a bit. Or, if it does not severely impact your business, ignore it.
Sources and links:
https://en.wikipedia.org/wiki/Pareto_principle
https://www.investopedia.com/terms/e/economicorderquantity.asp
https://abcofprocurement.com/how-to-use-the-critical-path-method-in-procurement/